hot-dip galvanized bolts – what is hot dip galvanized bolts – HDG bolts
What is hot-dip galvanized bolts and used for?
Hot-dip galvanized bolts are an effective metal anti-corrosion method, which is mainly used in metal structure facilities in various industries. The rust-removed steel parts are immersed in a molten zinc solution at about 500°C, so that a zinc layer is attached to the surface of the steel parts, thereby achieving the purpose of anti-corrosion.
The processing technology of hot-dip galvanized bolt
Hot dip galvanizing process: finished product pickling-water washing-adding auxiliary plating solution-drying-rack plating-cooling-medication-cleaning-polishing-hot-dip galvanizing is completed.
Advantages of hot-dip galvanized bolt after hot-dip galvanizing
Hot-dip galvanized bolts are durable after hot-dip galvanizing
In suburban environments, the standard hot-dip galvanizing anti-rust thickness can be maintained for more than 50 years without repair; in urban areas or offshore areas, the standard hot-dip galvanizing anti-rust layer can be maintained for 20 years without repair
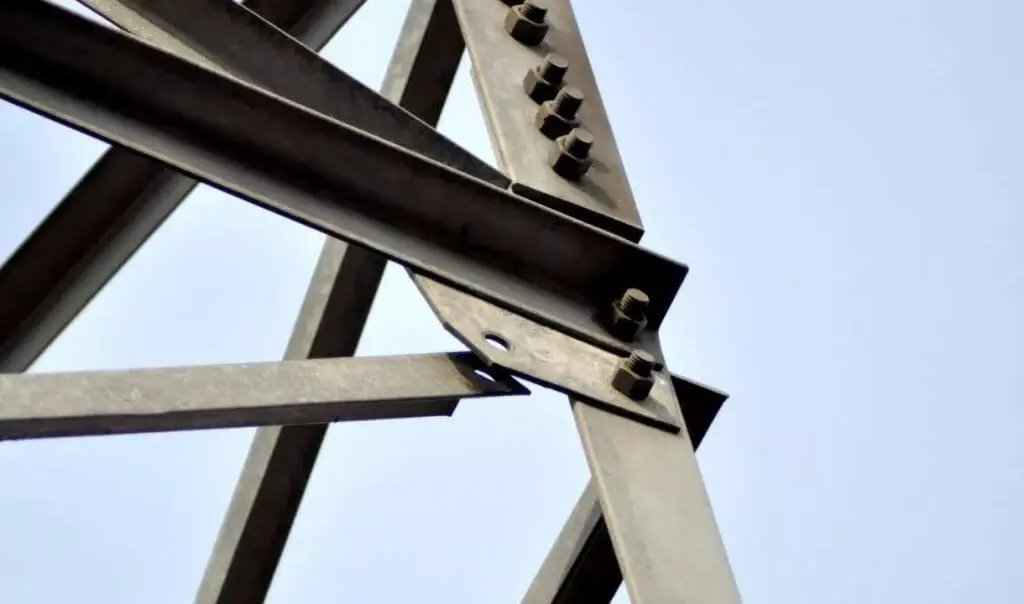
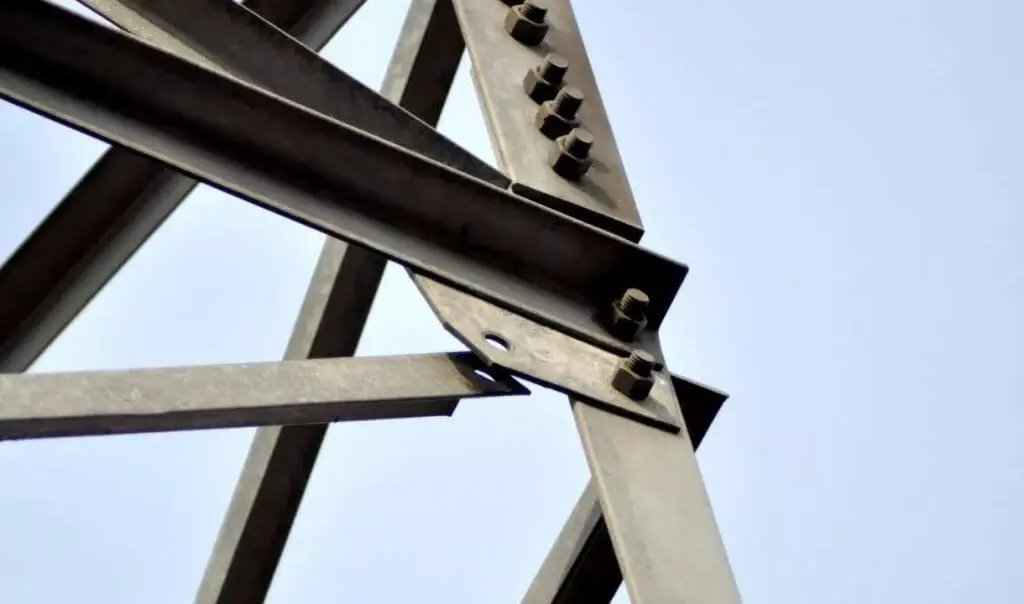
Low processing cost of hot dip galvanized bolts
the cost of hot-dip galvanizing anti-rust is lower than that of other paint coatings
Hot-dip galvanized bolt have good reliability
the galvanized layer and the steel are metallurgically bonded and become a part of the steel surface, so the durability of the coating is more reliable
It can save time and labor costs
the bolt surface treatment hot-dip galvanizing construction process is convenient and quick, one-time installation can be used for decades, and there is no need to repaint or spray paint during installation, and it does not need Maintenance of painting.
Strong toughness of the coating
the zinc coating forms a special metallurgical structure that can withstand mechanical damage during transportation and use
Comprehensive protection
every part of the plated parts can be plated with zinc, even in recesses, sharp corners and hidden places can be fully protected
Improve the performance of bolts
The most obvious benefit of HDG bolts is to improve the performance of the screws.
Performance grade of hot-dip galvanized bolt:
the quality of hot-dip galvanized bolts is 4.8 and 6.8, like 8.8; 12.9; 10.9 will be lowered when hot-dip galvanizing, so when purchasing hot-dip galvanized screws, be sure to consult clearly before placing an order. When purchasing hot-dip galvanized bolts, you must understand the grade of hot-dip galvanized bolts.
What is the thickness of the galvanized layer of hot-dip galvanized bolt?
The American Standard has completed a large number of tests for various screws and bolts, with medium-sized bolts (M6~M10), galvanized thickness of about 5-8 microns, appearance, and corrosion resistance without hydrogen embrittlement annealing; performance level of hot-dip galvanized ordinary bolts: 4.8- 10.9, specifications M12-M48. The thickness of the hot-dip galvanized coating is ≥ 54μm.
The selection is mainly based on the basic deviation of the accuracy of the thread. The surface treatment is generally based on customer requirements. The usual thickness of galvanizing is between 5-8 um.
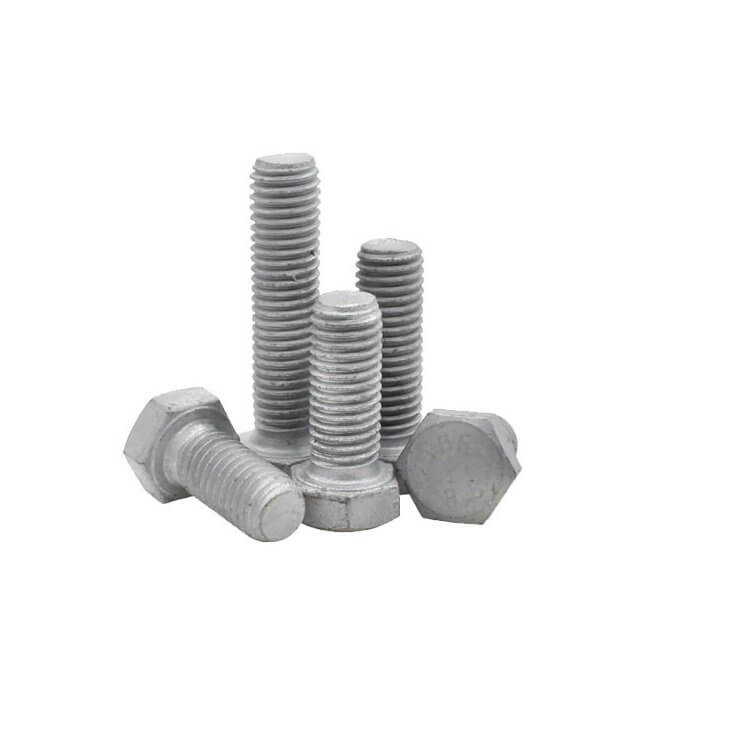
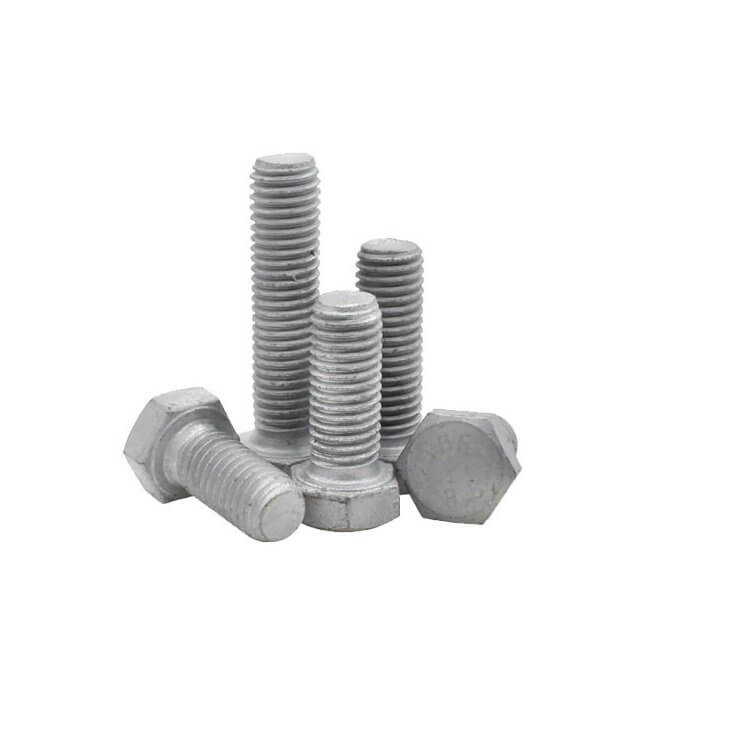
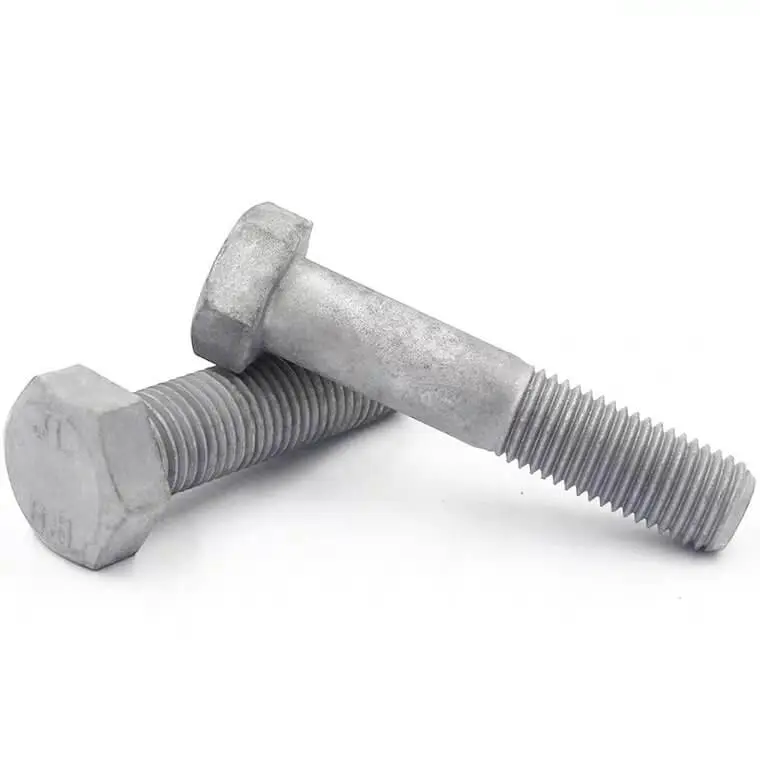
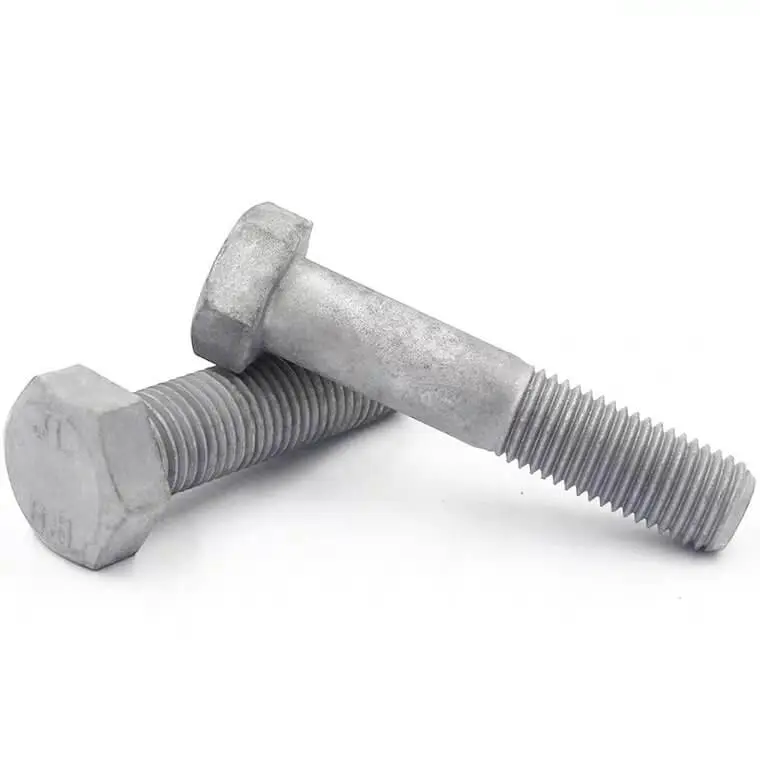
Hot-dip galvanized bolt used for
The coating of hot-dip galvanized bolts is thick, generally 30-60 microns, and the coating has a high anti-corrosion ability. Hot-dip galvanized bolts are very suitable for long-term rust prevention of steel parts exposed to work outdoors (such as highway and high-speed rail fence projects, large power towers, tunnel supports, and other relatively “rough” workpieces). Older iron water pipes were also hot-dip galvanized. In addition, due to high strength and corrosion resistance, hot-dip galvanized bolts are increasingly becoming the first choice bolts for power tower signal towers and highway guardrails.
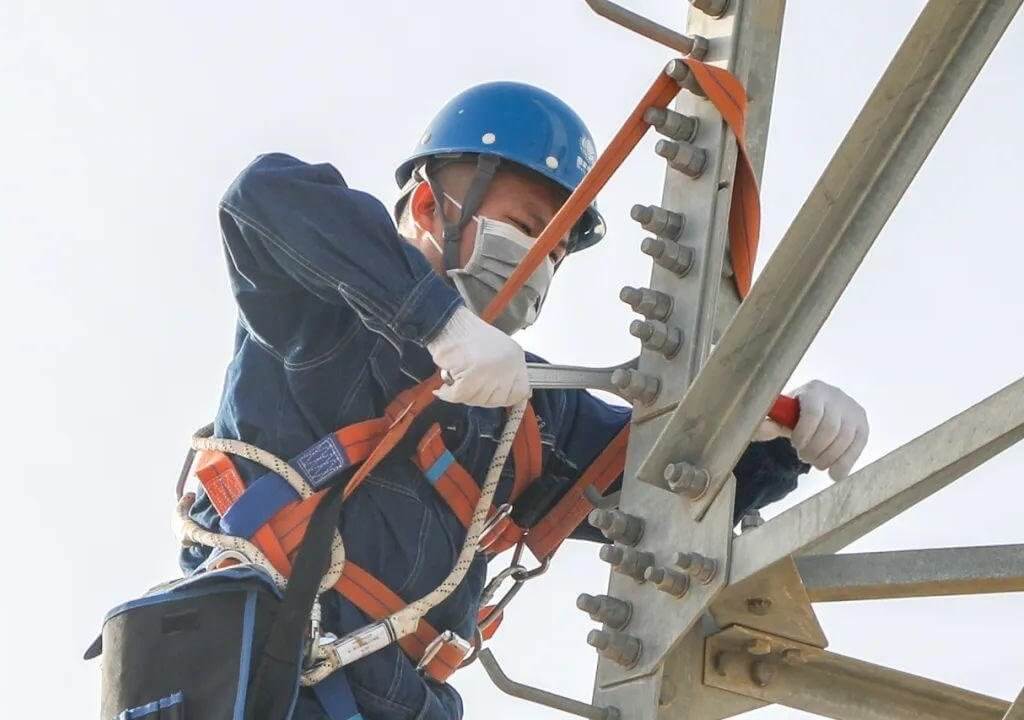
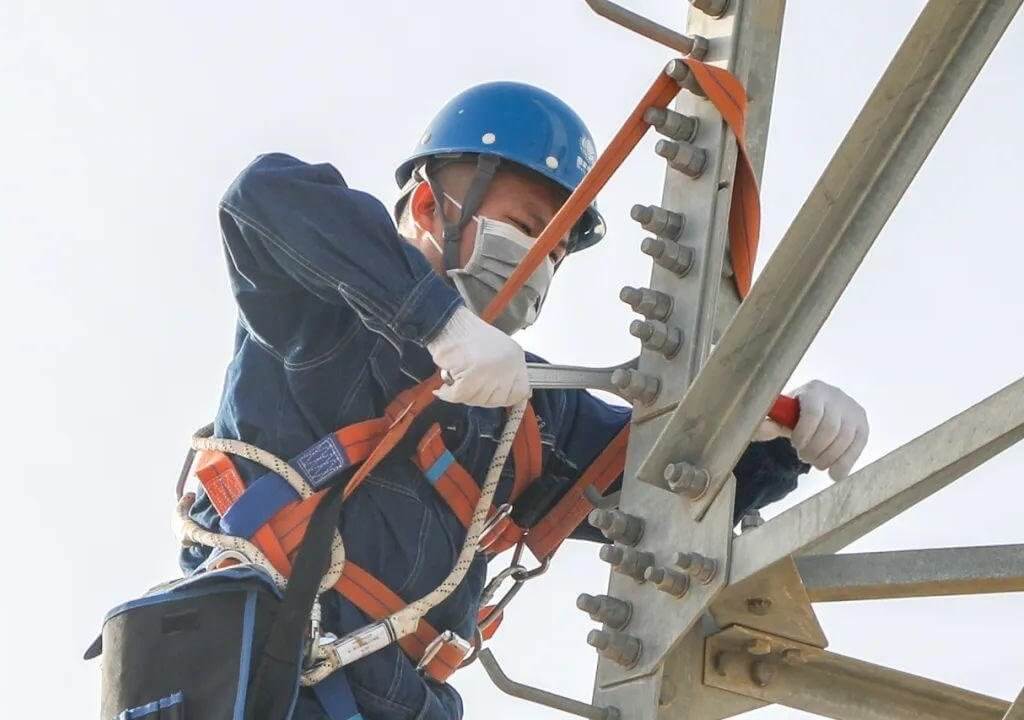
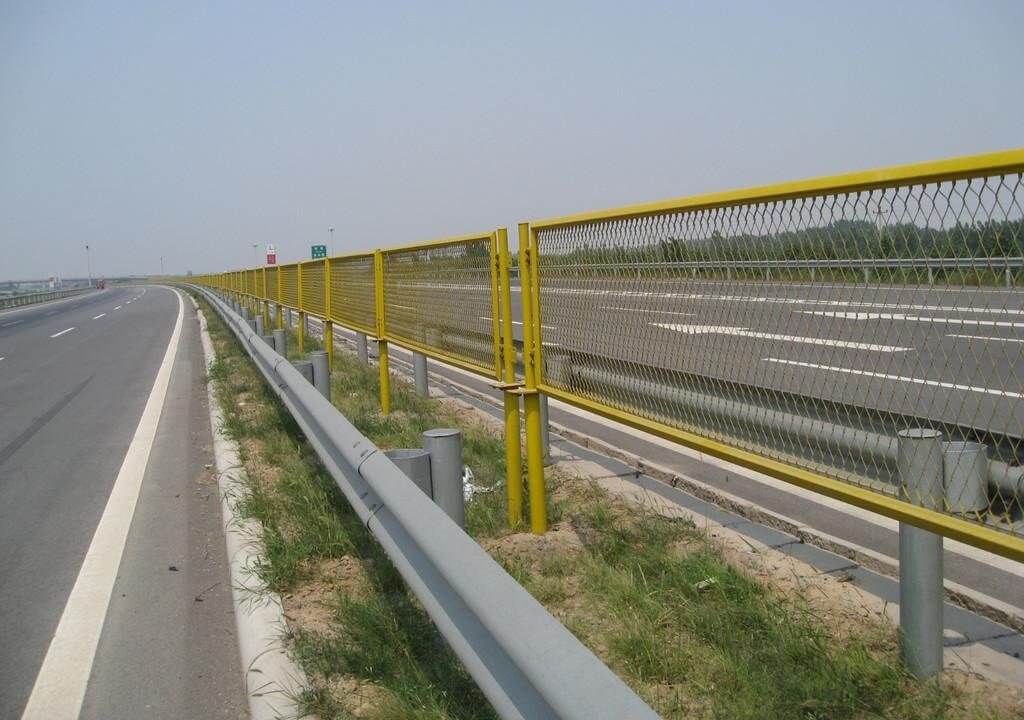
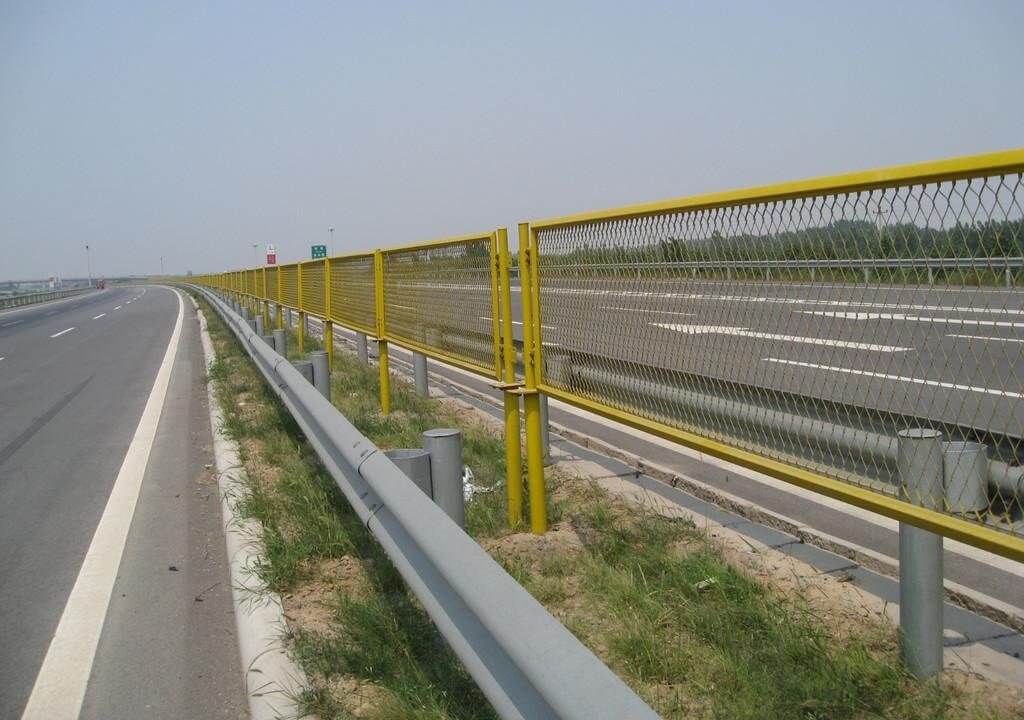
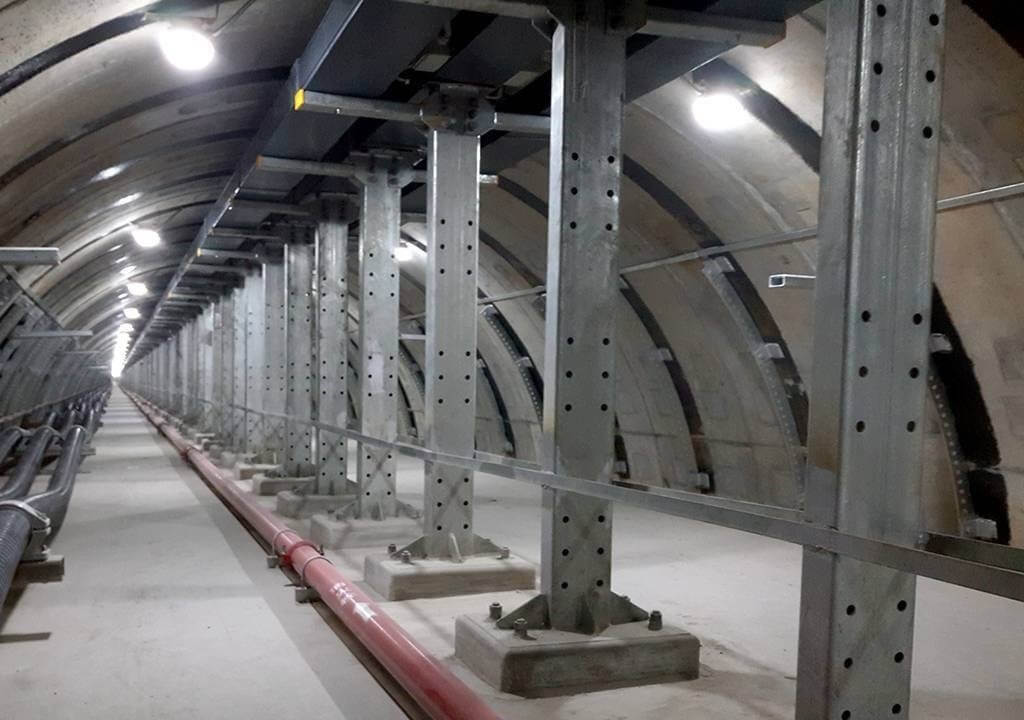
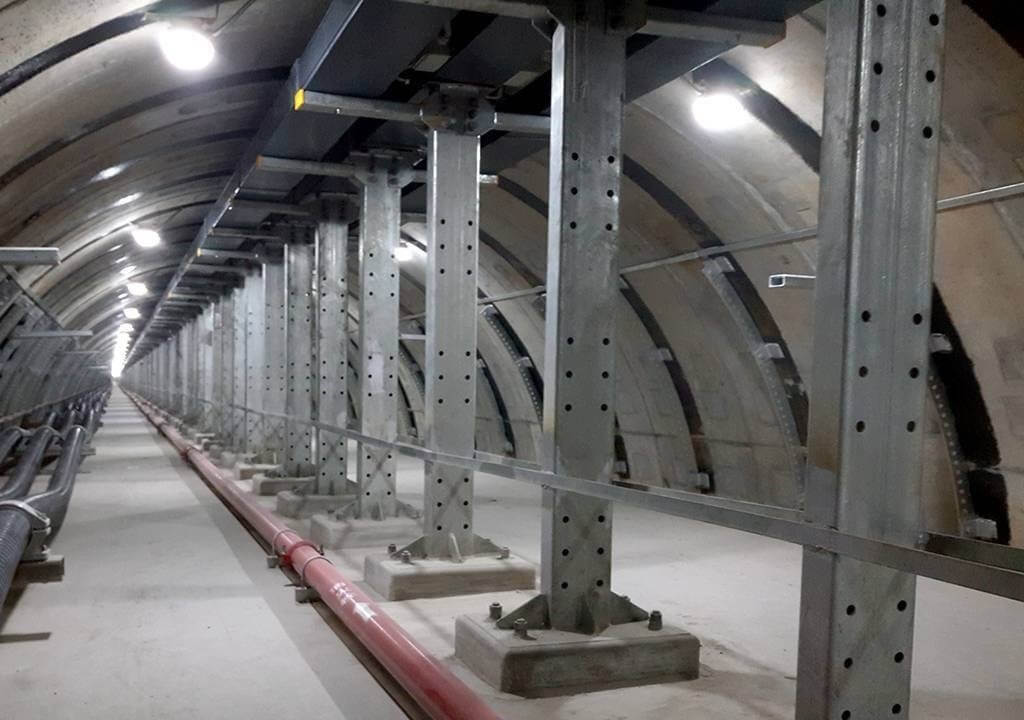
Description of the protective performance of the zinc layer of hot-dip galvanized bolt
The thickness of electro galvanization of ordinary fasteners is usually more than 5μm, while the thickness of the galvanized layer of hot-dip galvanized bolts in ordinary environment construction is more than 35μm, and the coating of hot-dip galvanized bolts working in harsh environments will reach 200μm. Hot-dip galvanized bolt have good coverage, dense coating, and no organic inclusions.
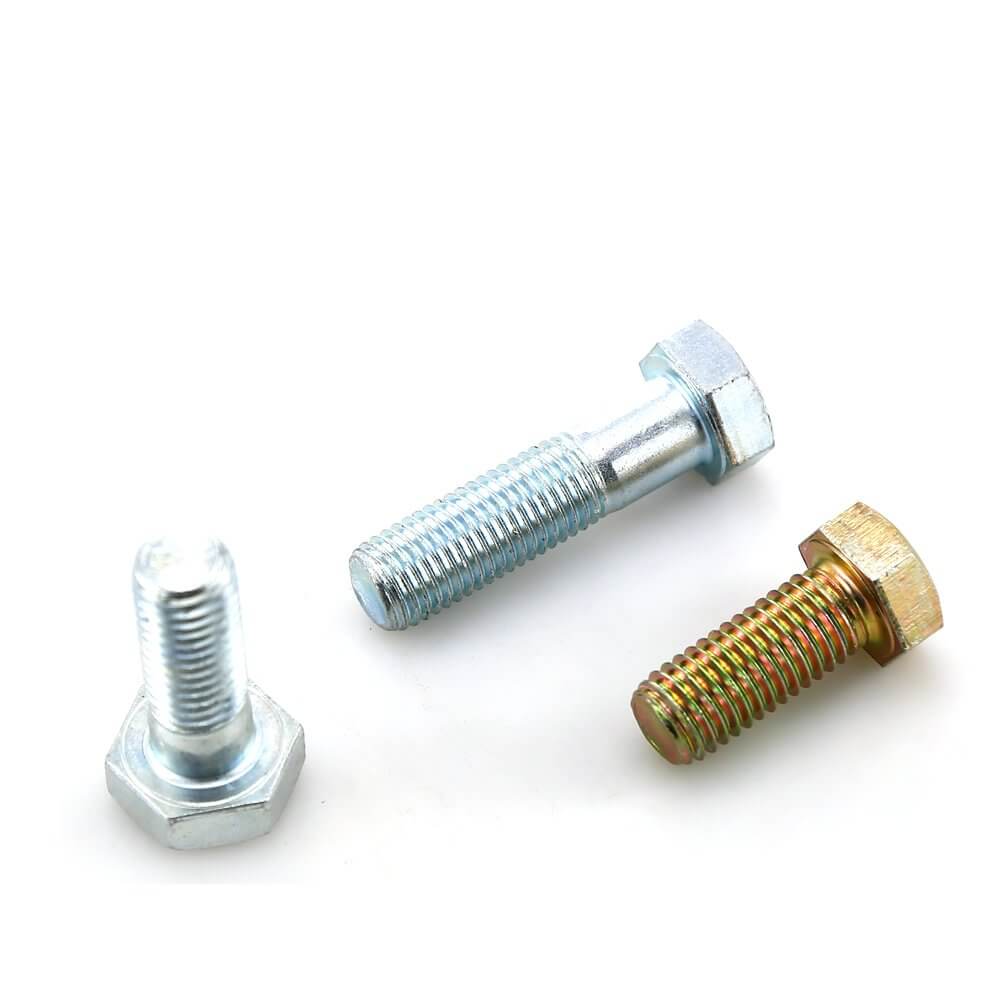
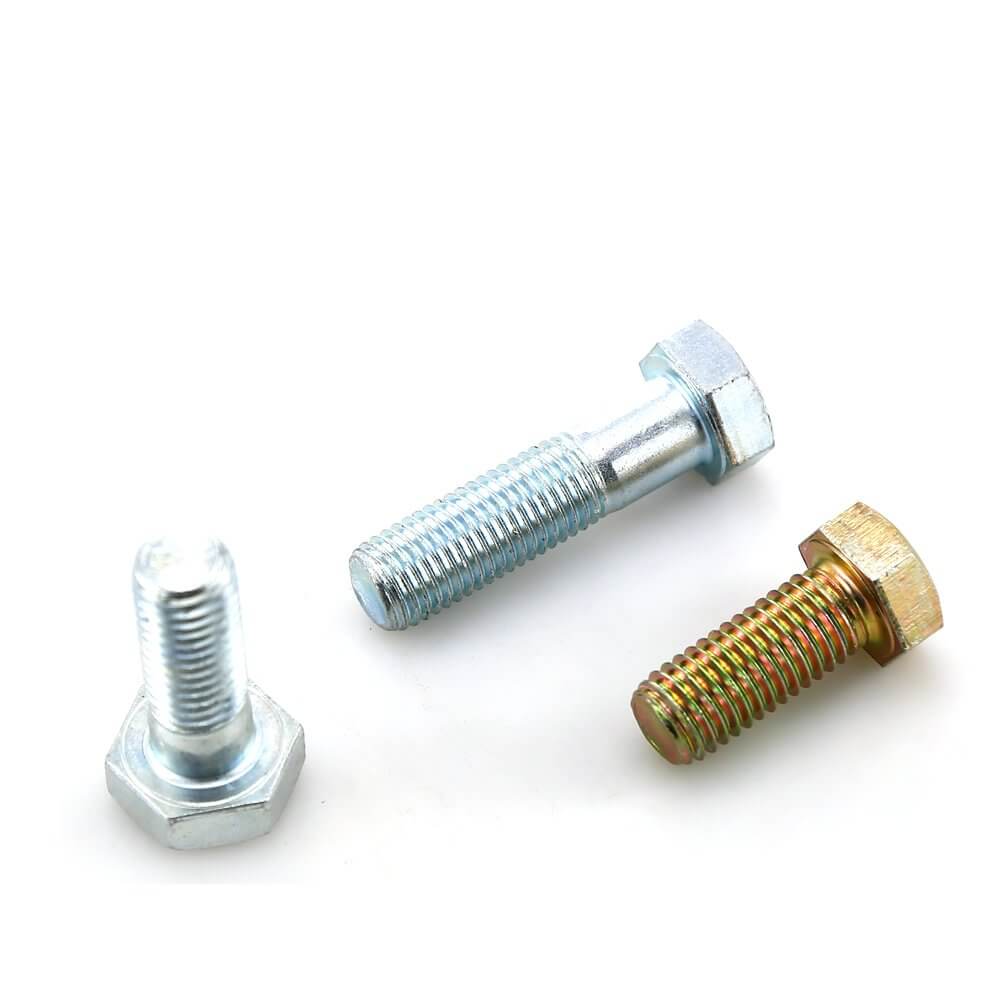
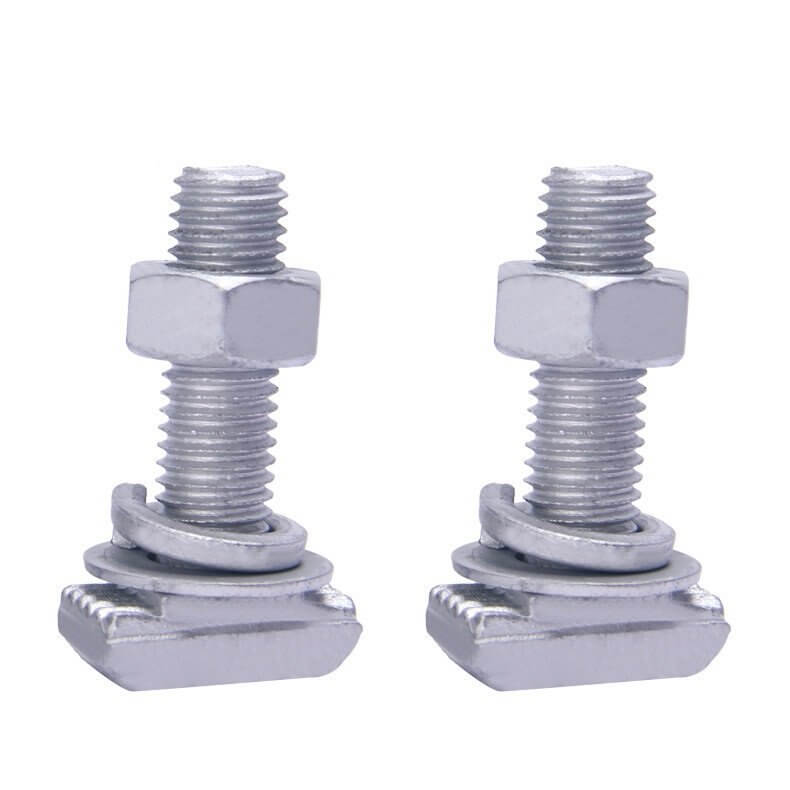
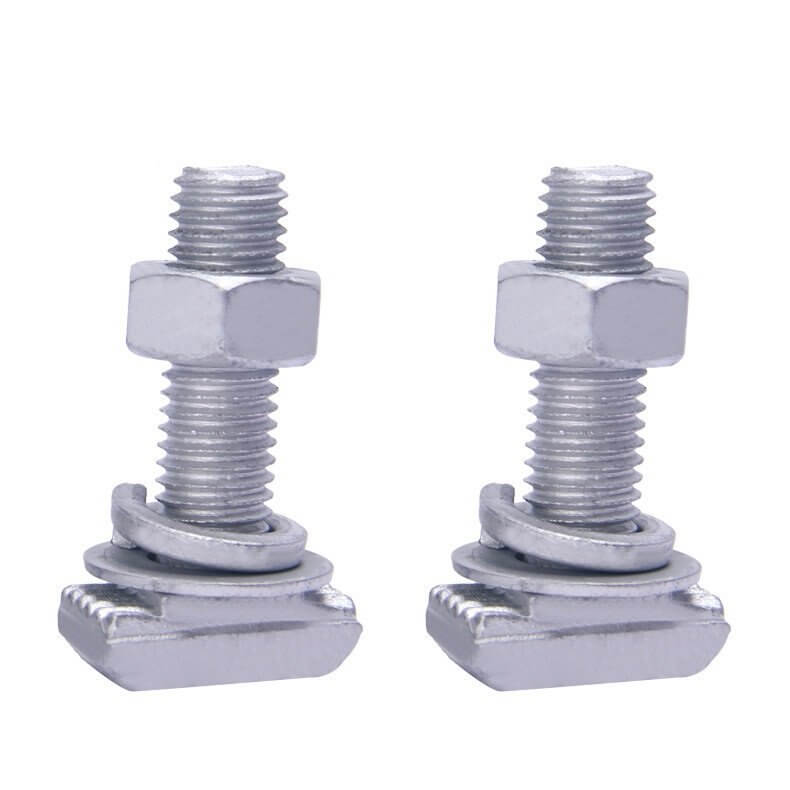
As we all know, the anti-atmospheric corrosion mechanism of zinc includes mechanical protection and electrochemical protection. Under ordinary environmental conditions, the surface of the zinc layer of hot-dip galvanized fasteners has a protective film of zinc oxide, zinc hydroxide, and alkaline zinc carbonate, which can completely corrode the thick hot-dip galvanized layer slowly. This corrosion process It can be ten or twenty years.
The protective film (also known as white rust) is damaged and a new film is formed. When the zinc layer is seriously damaged and the iron matrix is endangered, zinc will produce electrochemical protection for the matrix. Obviously, hot-dip galvanized bolts have better atmospheric corrosion resistance to base metal iron than electro-galvanized.